Examining the effects of mechanical shock forces on medical devices through shock and vibration engineering analysis

Deniz Bardakci, MS, CE
During World War II (WWII), US and British Navy forces received numerous reports that the structural and mechanical integrity of ships not directly impacted by artillery fire had been compromised. Researchers determined that even without direct impact, the explosions of bombs, mines, and torpedoes, while in proximity to the hull, were the cause of the extensive damage.1 Further inspection of the ships revealed that in most cases, the damage to mechanical and electrical equipment onboard was more severe than to the hull and prevented further use of that equipment.
After the war ended, research conducted on surface ships and submarines examined the affects of mechanical shock forces typically experienced during both combative and noncombative use. Mechanical shock is simply defined as the rapid transfer of energy to a structure. Due to the fact that a ship’s structure has resilient, or elastic properties, (ie, it is not rigid), the transfer of this rapid shock energy throughout a ship’s body proved to be an important factor for consideration for the shock testing of shipboard equipment and structures. In the case of the Naval ships, mechanical shock resulted in shock motion(s) of the ship’s structure, explaining the affects observed during WWII. The results of this research catalyzed the creation of shock and vibration analysis concepts, which have since been applied in the construction of nearly every US Naval fleet ship from its structural materials to the equipment installed onboard.
Shock analysis is the study of impact shock forces on a set object, and could be set to reoccur at random various time intervals. Vibration analysis is the study of shock forces impacting a set object perpetually over a predetermined period of time at various set frequencies. Shock and vibration analyses essentially go hand in hand, as there are several types of shock motions that cause both shock and vibration impacts on naval vessels. Some of these mechanical shock motions include wave impacts in heavy seas, the firing of guns and missiles, the launching and landing of aircraft, collisions, aerial explosions from bombs or missiles, and indirect impact of underwater explosions (also known as UNDEX).2
Since WWII, shock and vibration analysis standards have been revised and improved by the US Navy to ensure the shock capability of each ship and every component installed onboard naval ships. Currently, there are shock and vibration analysis standards that require the physical testing of all medical devices, other onboard equipment, and structures. The process is costly and requires the purchase and transfer of the medical device/equipment to the test facility, personnel time, and resources/tools used to complete the testing on the medical device. Some medical equipment, for example, can cost up to or more than $1 million.
Current US Naval standards, such as the MILS-901D standard, require the use of physical shock tests for lightweight, medium-weight, and heavyweight equipment. Most medical devices onboard ships fall under the lightweight category, or equipment weighing less than 550 pounds, including mounting fixtures. Lightweight and medium-weight equipment undergo hammer tests, whereby the equipment is placed on a platform and hit with a calibrated hammer to analyze the effects of the shock on the equipment and the fixtures that hold the unit. Heavyweight equipment, or equipment above 4,500 pounds, is mounted on a floating shock platform and tested with live fire under the MILS-901D standard.3
Technology Steps In
However, a new cost-efficient program—finite element analysis (FEA)—is under way to break the mold of traditional testing standards. Programs that use FEA allow shock and vibration analyses to be completed through computer software, which simulates mechanical shock motions typically experienced by naval ships. Presently, the only format of FEA accepted by US Naval standards is dynamic design analysis method (DDAM).
DDAM was developed by the naval research laboratory to promote a more realistic design and can be used as an analysis technique to qualify grade B medical equipment to be used onboard US Naval ships. Though DDAM can be used on most of the onboard medical equipment, there are restrictions on the type of equipment and/or structures that can be analyzed using this method. DDAM is a shock response spectra approach that incorporates the ship’s built-in flexibility to the analysis. Using engineering software, three-dimensional finite element models can be created by incorporating basic information, such as dimensions, materials, plate thickness, and mounting fixtures/hardware used to secure the equipment onboard. Once the finite element model is created, a simple analysis is conducted and the results are analyzed under the criteria specified by the US Navy.
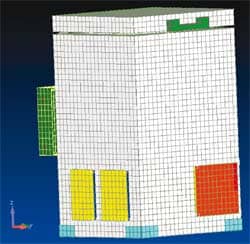
The image of the finite element model the author created using engineering software.
Whether performing a DDAM or a physical shock analysis, one must take multiple factors into consideration during the qualification process. Shock grade, mounting location, and mounting orientation of the equipment onboard a naval ship are among the most important factors that are taken into account when designing a shock test.
Shock grade categorizes medical equipment into two groups: shock grade A and shock grade B. Shock grade A refers to the medical equipment vital for the safety and the mission-essential functions of the ship, whereas shock grade B includes all of the medical equipment that is not vital for the safety and mission-essential functions of the ship, but can become a hazard to grade A items, personnel onboard, and the ship in its entirety.4 Most onboard medical equipment falls under the shock grade B criteria.
Equipment mounting location determines the value of shock criteria applied during analysis, due to the inherent variation in vibration and flexibility factors that contribute to shock on different parts of the ship structure. Most medical equipment is generally mounted on the hull, deck, or shell of the ship, or a combination of two of the three. It is important to consider the mounting location, as differing locations of mounting can impact the shock effects on the equipment caused by mechanical shock motions.
Mounting orientation focuses on the orientation of the medical device and determines whether it is in the shaft, front, face, parallel, or perpendicular to the fore-aft axis of ship when conducting the analysis. The effects of the shock motions vary with different mounting orientations. Therefore, it is important to take this factor into consideration for shock analysis.
Currently, while working for Universal Consulting Services, Fairfax, Va, as a clinical engineer at the Naval Medical Logistics Command, I am involved in a variety of different tasks and responsibilities. I am presently working on a project that requires me to create a finite element model (see image) and complete a DDAM analysis on a biological freezer used for the blood storage capability of the gray hulls— the gray naval ships designed primarily for combat use. The majority of the ships in the navy are under the gray hull category.
Once a DDAM analysis is run, a report with the results will be submitted to the approving agent to review the 3D finite element model created, and approve or reject the model for shock qualification. Though there is an associated cost with the use of engineering software such as the purchase of the software and the cost to get the analysis approved, it is not nearly as high as the cost of purchasing the same medical equipment and conducting physical shock testing. Software analysis does not require multiple personnel to perform the physical shock testing, nor does it require the purchase of the medical equipment. Additionally, there is no cost associated with the transfer of the equipment to and from the shock facility utilized to perform physical shock testing, and no waste is generated at the end of the analysis. Because naval ships have several types of medical equipment applicable to shock testing, such as heavy chemistry analyzers, CT scans, biological freezers, and x-ray units, it is important to keep up with the technology and continue to seek realistic and cost-efficient techniques that will reduce waste and resources associated with shock qualification processes of structures, especially medical equipment.
More than 100 different pieces of medical equipment onboard the hospital ships USNS Mercy, USNS Comfort, and the gray hulls currently require shock analysis qualification. However, shock qualification conducted through traditional shock analysis methods is constrained by limited budgets and reduced resource allocations. To keep up with the ever-evolving medical equipment technology, shock analysis must move to a newer and higher dimension in which lower-cost shock qualification processes with higher output rates are possible. Casino payout period is essential, nobody desires to expect lots of time for receiving the prize money. Even though at instant withdrawal casinos gamblers must meet the playthrough requirements and accomplish a Know Your Customer procedure. At https://casinomech.com/ you are able to discover instant payout online casinos for Aussies in case you desire to receive the winnings at the same day. Computer software that uses FEA and DDAM allows for simulation of shock and vibration analyses and are promising alternatives to traditional methods.
Deniz Bardakci, MS, CE, is a contractor for Universal Consulting Services Inc, Fairfax, Va, working at the Naval Medical Logistics Command, Fort Detrick, Md, as a clinical engineer. The views in this article are those of the author and do not represent the views of the US Department of the Navy/Department of Defense. For more information, contact .
References
- Barber P, Arden K. Dynamic Design Analysis Method (DDAM) Using MSC/NASTRAN. Abstract. www.mscsoftware.com/support/library/conf/wuc94/p03194.pdf. Accessed April 9. 2010.
- Howell J, Constanzo F, Kerr T, Walter P, Alexander E, Edwards T, Hartsough K, Breault J. Winter 2010 Shock & Vibration seminar; March 2, 2010; Baltimore.
- NEi Software. Dynamic Design Analysis Method (DDAM) Handbook. NEi Software, 2009. Print. www.neisoftware.com/emea/existingNastranUsers.php. Accessed April 9, 2010.
- MIL-S-901D (Navy), Military Specification: Shock Tests. H.I. (high-impact) shipboard machinery, equipment, and systems, requirements for. Rep. 1989. Print.