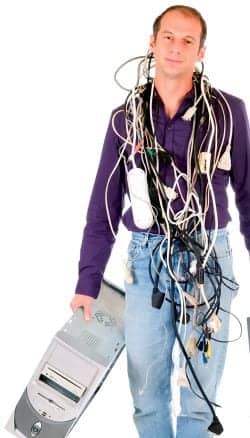
Interested in changing the way you look at electronic troubleshooting? The list I have compiled had an unusual beginning, but it has changed the way I troubleshoot electronics—from the everyday simple problem to the extremely complex.
When I started in electronics in the advanced electronics field in the US Navy, I took care of inertial and satellite navigation and other assorted electronic systems in submarines. As a beginner in troubleshooting these complex systems, I was struck by the number of times complex failures were caused by really simple things—like a blown fuse or a loose wire. With my curiosity aroused, I began to keep a list of the simple causes. As the list grew, I began to use it as a screen before I got too deep into the classic electronic troubleshooting techniques. As I gained experience, I realized that about 80% of fixes came from using the list, and I completed most troubleshooting in 20 minutes.
While many troubleshooting methods exist to find the cause of equipment problems, most find a basis in investigative methods, analysis of circuits, and logic. When it comes to troubleshooting, listening is a valuable skill that can also be applied to any investigative endeavor. Admittedly, classic troubleshooting has gaps. Due to the proliferation of classes and models of devices, it is not possible for any one person to have training in all aspects of all devices. Clinical/biomedical engineers often find themselves confronted with an unfamiliar piece of equipment bearing a sticky note saying, “broken” or “X” on their desk—with no user to interview or documentation to consult. And, by the way, they need it in 20 minutes.
When I get a chance to question a system expert, I ask, “What are the 10 most common failures of your product?” I have always gotten a list of common and easy fixes that get filed under device-specific troubleshooting. Our helpful engineer gets a reduction of nuisance service calls, and I get more effective. Here, find 10 tips that help get to the root of problems you may encounter.
1
Is it Plugged In?
I gave a kid-friendly version of this presentation to middle-school children at a science fair called, “How to Become an Electronic Genius in 10 Easy Steps.” Sometime later, frustrated coworkers with a dead computer mystery confronted my wife. Remembering the presentation, she ducked under the desk to see if it was plugged in. It had somehow become unplugged. She corrected the situation, the computer booted up, and from that point on she became the go-to person for all computer problems.
This item covers not only the power cord, but also all the signal and power cords in the system of interest. In the typical computer there are at least a half-dozen cables that can be accidentally pulled out, lose a retainer, or be incompletely seated just enough to cause intermittent operation. Check and firmly seat all plugs.
2
Is it Turned On?
Medical equipment often has more than one switch. There is usually a switch in the front, and then there is often a switch in the back next to the AC power cord entry and fuse. Sometimes this switch is off, and if the equipment has a battery, the absence of AC is not noticed until the battery has run down to damagingly low levels.
Another point covered here is one of the common cure-alls for modern equipment—the “off-on” reset. Turn the device off, wait 5 to 10 seconds for the power supplies to discharge, and then turn the device back on. This often works to clear an error state that has occurred during operation due to a power transient or poor grounding.
The third point to consider is whether there are any safety or limit switches that keep the equipment from turning on or operating. An activated or stuck limit switch can stop the show.
3
Is the Plug Good?
Lack of proper installation of the Belden green-dot hospital-grade plugs has been disproportionately responsible for power losses and intermittent operation in portable equipment. If you shake the plug and get a little rattle, the wires are not screwed down tightly. Loose plug wires produce crazy problems. Check that no insulation is in the bare wire terminal clamps and that no one has tinned the wire ends with solder. Tighten down the terminals, and this crazy is cured. If a plug has overheating damage (melting or traces of smoke deposit), replace it with a higher-rated plug and check for Item 4.
4
Is the Wall Socket Live and Solid?
Loosely mounted, damaged, smoke-stained, heat-damaged wall outlets are likely to be dead or intermittent. Check with an outlet tester or use another outlet on another circuit until you can properly check the suspect outlet and circuit.
5
Is the Wire Next to the Plug Good?
Any plug that is handled often will develop wire breaks and connector damage. If the suspect is an AC plug, cut off 6 inches of wire and reterminate. If the suspect is a signal plug, mount the plug in a vise and check continuity while pulling and twisting the cable.
6
Blown Fuses?
Fuses are usually easy to check, but sometimes they are found in the strangest places. Is the fuse the correct amperage and type? Why did the fuse blow? Study fuseology—it is fascinating.
7
Is There a Battery? Is it Good?
Battery technology had a huge head start in ancient Egypt and Persia, but it has not kept pace with modern electronic advances. Batteries are the most problematic components in electronic systems. Look for bulges and burns, and check voltages from cell to cell to look for shorted cells (0.00V) or low cells. A bad battery will produce low voltage that is a multiple of the basic cell voltage. For example, a good 12V lead-acid battery will read about 13.7vdc, but a bad one will be about two volts low—the voltage of an individual cell that is not producing. Ni-cad batteries have the worst reliability. Bad batteries can drag down circuits to no operation even if the device is operating in AC mode.
Another issue with batteries is connection quality and tightness. With the battery’s low voltage, a loose or corroded connection will drop a significant amount of voltage. The battery will exhaust quicker and will not fully recharge, sustaining damage to individual cells. Typical cell voltages: alkaline 1.5V, Ni-cad 1.2V, lead acid 2.0V, Nickel metal hydride 1.2V, lithium 3.0V, lithium ion 3.6V.
Relay and switch contacts often get pitted and dirty and will not conduct full voltage. Replace the relay or switch, or disassemble and burnish resistive contacts.
8
Any Dead Fans?
Dead or slow fans will allow electronic components to overheat and fail hard or fail intermittently. Slow fans will often squeal from a dry bearing, and overheated electronic components age very quickly. A simple test for fan quality is to turn the power off and see if the fan coasts to a smooth, normal stop. If it does not, replace it. Fans are cheap—electronic boards are not.
9
Got Dirt? Any Dirt in Filters or Heatsinks?
I have yet to find an electronic schematic that included dirt. What is the schematic symbol for dirt? Dirt is variously abrasive, heat trapping, or electrically conductive. It is surprising how fast cooling airflow drops off with even a slightly dirty air filter. It is one of the open secrets that high-component-density devices like ultrasounds will operate flawlessly forever if the air filters are kept obsessively clean. CT slip rings do not like dirt and produce noisy data. Dirt-choked heatsinks kill components like CPUs and power supply heatsinks. Heatsinks should always have thermal grease or thermal pads in the mount—messy, but a must. I do not know how many times I have opened a flaky computer and found an interior that looked like the inside of a vacuum-cleaner bag. Clean it out, and it works perfectly again.
10
Use Error?
Use error gets a lot of blame, but it is actually rare. It only appears with a new piece of equipment or a new user. Often, the user knows how to operate the equipment better than we do. If possible, have the user operate the device to show the problem. In a true case of operator error, the fixes are: posting a printed notice on the device, keeping an operator’s manual available, and conducting a remedial in-service for recurring problems.
So now you have my list of 10 common-sense troubleshooting tips. The list will change as technology advances and manufacturers cure some of the problems. Some of the items will become more important or less important depending on circumstances and the type of equipment. I also have found that the less technical items have worked for nonbiomed people like physicians and nurses. It is amazing to see the broad, beaming smiles when a nurse has independently fixed a balky piece of equipment all by herself—it is a feeling of power.
David Meador, CBET, has worked in technical and medical technology fields since 1975. He is a biomedical equipment support specialist at Edward Hines Veterans Administration Medical Center, Chicago. For more information, contact .